We have a 1985 E32-3.
Found oil in our bilge. It wasn't coming from the engine. Eliminated all sources except the portion of our fuel tank that is concealed from view under the boat's liner pan.
The tank was about half full, too heavy for me to lift out in order to inspect the bottom. Called Precision Fuel Solutions www.precisionfuelsolutions.com (a Seattle-area company that services fuel systems), to see if they could pump out the tank and store its contents while I looked underneath. Les Newell at PF offered to inspect below the tank using his borescope camera, and also told me that his company could epoxy-line the tank to stop leaks. “When we get done, it will be an aluminum-reinforced fiberglass tank”.
The borescope inspection revealed that the lowest corner of the tank was corroded through. We agreed that PF should proceed with the tank lining. To save cost, I disconnected the tank then called PF to pump out my fuel and remove the tank for repair at their shop. Two weeks later, they returned the tank together with a 10 gallon jerry-can containing my fuel. I reconnected everything, dumped in the fuel, and fired up the engine.
Now I'm dealing with the oil in the bilge, which is trapped in all of the concealed crevices of the liner grid. Sailing around with bilge-cleaner and about 10 gallons of water, then pumping into buckets and disposing on shore. Rinse and repeat.
PF coated the tank, inside and out, with epoxy. The outside skin is glass-fiber reinforced. Cost about $800. I didn't look into the cost to have a welding shop patch the aluminum tank, but suspect that it would have been similar and I'd still have needed to pump out and store my fuel. This way, I got what is effectively a new tank. Seemed like the way to go.
Below: Here is a photo of the corroded tank...
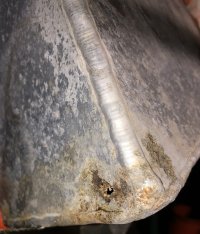
Below: Tank as returned from PF. Fiberglass-reinforced epoxy coated.
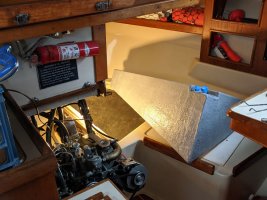
Below: All buttoned up!
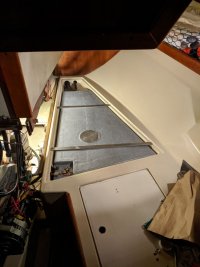
Found oil in our bilge. It wasn't coming from the engine. Eliminated all sources except the portion of our fuel tank that is concealed from view under the boat's liner pan.
The tank was about half full, too heavy for me to lift out in order to inspect the bottom. Called Precision Fuel Solutions www.precisionfuelsolutions.com (a Seattle-area company that services fuel systems), to see if they could pump out the tank and store its contents while I looked underneath. Les Newell at PF offered to inspect below the tank using his borescope camera, and also told me that his company could epoxy-line the tank to stop leaks. “When we get done, it will be an aluminum-reinforced fiberglass tank”.
The borescope inspection revealed that the lowest corner of the tank was corroded through. We agreed that PF should proceed with the tank lining. To save cost, I disconnected the tank then called PF to pump out my fuel and remove the tank for repair at their shop. Two weeks later, they returned the tank together with a 10 gallon jerry-can containing my fuel. I reconnected everything, dumped in the fuel, and fired up the engine.
Now I'm dealing with the oil in the bilge, which is trapped in all of the concealed crevices of the liner grid. Sailing around with bilge-cleaner and about 10 gallons of water, then pumping into buckets and disposing on shore. Rinse and repeat.
PF coated the tank, inside and out, with epoxy. The outside skin is glass-fiber reinforced. Cost about $800. I didn't look into the cost to have a welding shop patch the aluminum tank, but suspect that it would have been similar and I'd still have needed to pump out and store my fuel. This way, I got what is effectively a new tank. Seemed like the way to go.
Below: Here is a photo of the corroded tank...
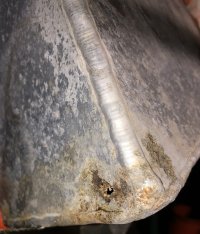
Below: Tank as returned from PF. Fiberglass-reinforced epoxy coated.
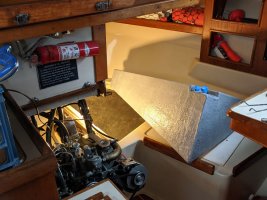
Below: All buttoned up!
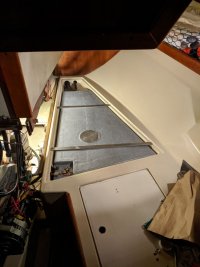