Update
Compression test: Looks OK, I guess. I found a Pittsburgh diesel compression checker for $30 at Harbor Freight. I used the glow plug adapter. Problem is, unless you can get the injector tubes off the injector pump, you can't get to the forward glow plug. My fuel tube nuts are stuck on the injector output nuts and I didn't feel like dealing with the springs and innards of the injector pump outlets in that environment (paint chips). So I did that forward cylinder with the M24 x 2 injector adapter and it acted about the same, but the fitting isn't a great way to do it with the tester kit components. The injector adapter either bottoms out on the head or, of you use the spacer, it won't engage enough threads. The adapter is softer than the head and will strip. I made a video of the runs, since the gauge or the hose or fittings aren't holding pressure well. After about 8-10 compression hits, the gauge reaches 300 on each cylinder. Keep in mind this is a cold engine and I can't run it. I wasted too much time struggling with the injector tubes where there is no room to work. Oh, and the engine wouldn't turn over initially. I think it was a loose or dirty solenoid connection. I used the house batteries to do the tests.
Head removal: The rocker arm shaft and rockers came off easily. Need a 12mm deep socket. The valve lifters show some wear on the bottom end, as expected. Still need to look at them carefully. They are not hydraulic, they're solid. I was able to get the head bolts loose with relative ease (!) using a 3/8 drive ratchet with a 4" cheater. The ones at the rear that were not under the valve cover (and not bathed in oil) were the toughest. One had the washer broken and was quite rusty and hard to turn. I had to use the 1/2" drive with a short cheater to break that one loose. Penetrating oil would have helped but I didn't stop to spray any. The bolts under the valve cover were easiest. At the rear corner of the head on the intake side is a coolant port, so that is a plug with a gasket, rather than a head bolt.
Prepping to lift the head involved some miscellaneous work.
1. I should have flushed the rest of the coolant out of the head, but didn't think of it until the head was broken free and it drained out. I'll probably have to vacuum out the oil pan.
2. Removed the exhaust flange from the exhaust manifold. Using penetrating oil (Bolt Blaster) made the job easier on the three nuts. I enclosed a picture of the carbon build up from the 10 seasons we've used the boat. My custom SS elbow collected some souvenirs of those years. Can't wait to see how much carbon I can't see. I need to clean that out every couple years. I have noticed a drop in power.
3. Remove the negative cable (ground) from the exhaust manifold.
4. Remove coolant hose from rear of exhaust manifold. Also remove coolant hoses and thermostat from front of engine.
The head broke free easily with a little effort with a small nail lifter bar. One of those crooked ones that carpenters use. The head and manifolds are heavy and I'll have to prop it up with some shims or starboard as I raise it. It has to lift about 4 inches straight up before I can muscle it out of there over the two studs.
I had to use the shop vac quite a few times to collect the paint chips. There are three colors of paint. Red, which seems to be the original or primer color, blue and Universal gold.
The 8th and 12th bolts from the left show a lot of soot. They are from near the injector ports.
The carbon build up of 10 cruising seasons inside of the SS exhaust elbow, near the water injection fitting.
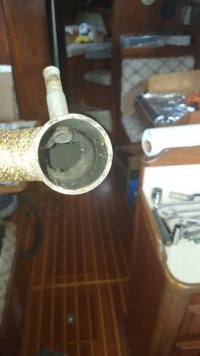