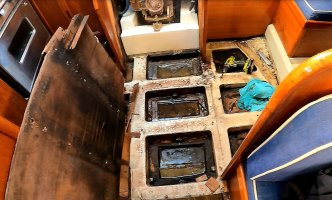
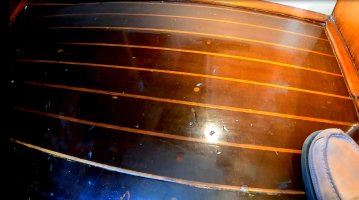
TAFG exposed; plug lines in sole.
The Ericson 381 sole is 3/4 teak and holly veneer. It is screwed down into the glass of the TAGF with two courses of 3/4 stainless screws per panel, meaning about 30 such screws in the companionway landing. The cabin entire has about 50 such screws.
The sole is trimmed with 34 individually fitted teak pieces. ,All are screwed down, for a total of about 75 screws. The trim screws into the plywood.
Every single one of those screws, excepting the periphery under the trim, is plugged. (To remove the sole you drill out the plug with a forster bit, find the exposed screw head, clean it with an Exacto knife, and extract.
To remove all trim pieces and one of seven sole panels took 8 hours.
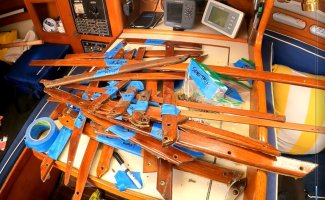
Was this ever a "removable sole"?
Nope. Given the number of screw and plugs, a brand new sole would be disfigured if not ruined even if the removed the next day.
But--soles should be removable!
Yes, but this one ain't. The E32-3 sole is 1/4 inch plywood and if screwed down can be easily lifted to inspect the entire bilge. I removed that entire sole twice at sea. Ericson did glue it down on some models, which was a mistake, and required destruction when replacing. Few owners glue down a new 32-3 soles, since screws work so well. And that model requires no trim.
But if you glue down the E381 sole it will never come up!
Well, it won't "come up" in any case.
Moreover, the new plywood must be made waterproof using several coats of CPES and or epoxy (I haven't decided yet).
To install the new sole with 50 plugs in it--what's that do to the waterproofing job? The holes are drilled after CPES and varnish. Any membrane is therefore violated. Plus, plugs into pre-varnished plywood have no varnish on them, and will never have the seven coats prescribed.
The large number of screws used on the E381 were intended to lock the floor to the boat.
A glued-down sole would be equally anchored and immobile.
A glued-down sole would mean no lines of plugs, a great saving in labor time (many of the existing plugs have no screws under them because the factory guessed wrong about location and had to drill another hole half an inch away to find a holding surface).
I can screw the plywood into the TAFG at the edges, as the factory did. Since those screws are under the trim, they need no plugs.
In sum, the drawback to a glued-down sole is that it can never be removed.
But the E381 sole, as factory constructed, was never intended to be removed.
Access is through generous inspection ports. And so far it looks like on this model there are no hoses or wiring under there in need of future service.
Find a flaw in the argument, please. I can't.