Thought I'd share a few photos of my hatch build for posterity's sake... It was a daunting project, which took about 2 weeks to complete, and I would have never attempted to do it myself if it weren't for the info I found on this invaluable forum!
My old sliding hatch was weathered, termite-infested, and eventually collapsed under my weight.. in other words, totally irreparable. However, I kept it as a template for the new one and was able to salvage the top slats. The most frustrating part of this project was framing and fitment, but as the centerpiece of the boat it was well worth the effort.
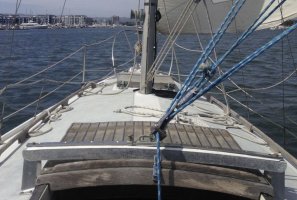
The base: I started by building a strong back frame/sandwich/mold, which followed the arch of the existing hatch. I then laid 2 overlapping pieces of 1/4" marine-grade plywood on top of the frame, which were glued together using epoxy with adhesive filler and then pressed to form with whatever heavy I had on hand. I made sure the base had at least 1" of overlap on all sides. Upon curing, it felt very strong under my weight and had very little spring-back, luckily.
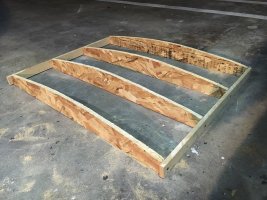
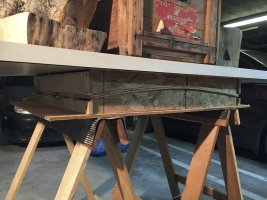
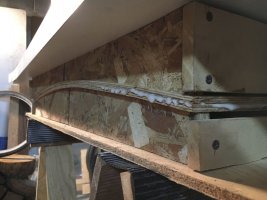
My old sliding hatch was weathered, termite-infested, and eventually collapsed under my weight.. in other words, totally irreparable. However, I kept it as a template for the new one and was able to salvage the top slats. The most frustrating part of this project was framing and fitment, but as the centerpiece of the boat it was well worth the effort.
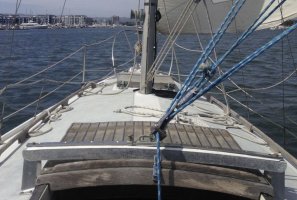
The base: I started by building a strong back frame/sandwich/mold, which followed the arch of the existing hatch. I then laid 2 overlapping pieces of 1/4" marine-grade plywood on top of the frame, which were glued together using epoxy with adhesive filler and then pressed to form with whatever heavy I had on hand. I made sure the base had at least 1" of overlap on all sides. Upon curing, it felt very strong under my weight and had very little spring-back, luckily.
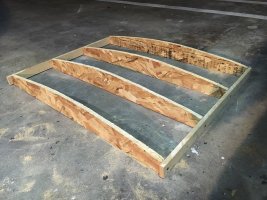
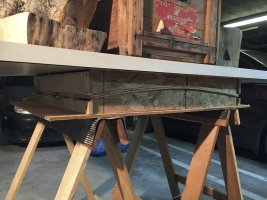
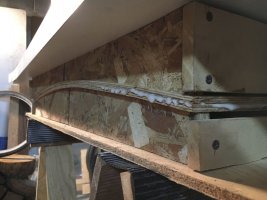
Last edited: