While I wait to address engine issues, (of course) I've stumbled upon another issue. While checking my fuel pickup down in the lazarette, I noticed that the hose coming from our electric bilge pump (the red hose in the picture) essentially plunges straight down from the through hull and doesn't have an anti-siphon loop. There is just about a foot of freeboard between the through hull and water level when we're not underway. However, when there or four of us in the cockpit, going 5-7 knots, the stern dips such that the waterline will often partially or fully cover the through hull. Methinks the absence of an anti-siphon loop may explain why we'll get water in the bilge sometimes while underway.
Is this (or something else related) a plausible reason for water in the bilge? Does anyone else, particularly E30+ owners, have a similar arrangement with the electric bilge pump hose through hull, but with an anti-siphon loop? Without one, and not getting any water?
I swear, every day a new discovery!
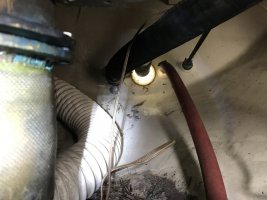
Is this (or something else related) a plausible reason for water in the bilge? Does anyone else, particularly E30+ owners, have a similar arrangement with the electric bilge pump hose through hull, but with an anti-siphon loop? Without one, and not getting any water?
I swear, every day a new discovery!
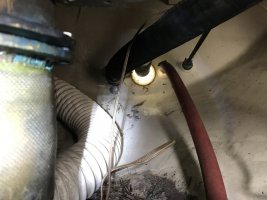