EricFox
Member II
Thought I would show details of what I did since I couldn't find a lot on the forum before I embarked on this project.
In previous winters the mast has always come down. But it's a lot of work. And an opportunity for things to go wrong - last year the yard bent my furler due to their error in lifting it off the mast rack. So this year I have left it up. But I get a lot of rain water down the inside of the mast which will freeze come December, so I did what a few C&C and CS owners at our marina have done and drilled a drain hole through the hull to the bilge and installed a brass garboard drain (one boat failed to do this one winter and visited the boat mid-winter to find the ice up to the cabin sole - sudden mid-winter project to remove the sole!).
A few comments and pictures to help others who want to do the same in future.
- pilot hole drilled from the inside (main bilge compartment), then 1" hole drilled from the outside
- the centre of the hole is ~0.5" above the floor of the bilge (see pic) which puts the bottom the hold flush with the floor of the bilge
- the hole is angled down very slightly (maybe 10 degrees) to the outside
- the bottom of the hole ends up being ~1-3/8" above the keel/hull joint (see pic with measuring tape)
- that puts the brass drain on a mostly flat surface - the curve as the hull pulls away from the keel is just starting at the top of the fixture - ideally I would have drilled the hole ~1/4" lower to be fully on a flat surface, but then I wouldn't have had room for the nuts on the inside (bottom bolt holes would have been at or below the floor of the bilge) - to make the surface of the brass drain as slush as possible to the hull surface I filed the hull side the brass drain away at the top
- note that there is no air gap between the hull and the grid (interior wall of the hole) - I was expecting a small gap based on a picture that I saw in another post
- I applied a layer of epoxy on the walls of the hole to create a water tight seal for the portion without the brass insert
- I was concerned that screws might break the fiberglass so I opted for #8 bolts (1.5") with the buts on the inside of the bilge to hold the fitting to the hull - everything sealed with 4200
- I finished off with a removable screen on the side to keep critters out during the winter - sorry, forgot to snap a pic from the inside showing the bolts and the mesh screen
I'll let you know if everything is water-tight when I launch next spring.
Hole as seen from the outside - the hole is ~1" deep (hull + grid)
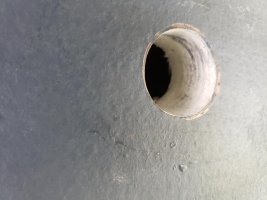
Hole from the outside showing proximity to the keel/hull joint (faint line at the 3" mark on the tape)

From the inside - the bolt is the forward port keel bolt in the main bilge compartment - holes for the 3 bolts not yet drilled
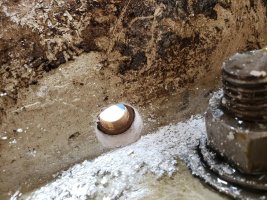
From the outside with 4200 sealant
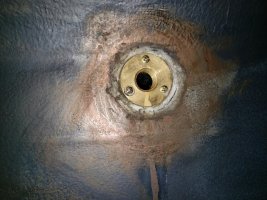
In previous winters the mast has always come down. But it's a lot of work. And an opportunity for things to go wrong - last year the yard bent my furler due to their error in lifting it off the mast rack. So this year I have left it up. But I get a lot of rain water down the inside of the mast which will freeze come December, so I did what a few C&C and CS owners at our marina have done and drilled a drain hole through the hull to the bilge and installed a brass garboard drain (one boat failed to do this one winter and visited the boat mid-winter to find the ice up to the cabin sole - sudden mid-winter project to remove the sole!).
A few comments and pictures to help others who want to do the same in future.
- pilot hole drilled from the inside (main bilge compartment), then 1" hole drilled from the outside
- the centre of the hole is ~0.5" above the floor of the bilge (see pic) which puts the bottom the hold flush with the floor of the bilge
- the hole is angled down very slightly (maybe 10 degrees) to the outside
- the bottom of the hole ends up being ~1-3/8" above the keel/hull joint (see pic with measuring tape)
- that puts the brass drain on a mostly flat surface - the curve as the hull pulls away from the keel is just starting at the top of the fixture - ideally I would have drilled the hole ~1/4" lower to be fully on a flat surface, but then I wouldn't have had room for the nuts on the inside (bottom bolt holes would have been at or below the floor of the bilge) - to make the surface of the brass drain as slush as possible to the hull surface I filed the hull side the brass drain away at the top
- note that there is no air gap between the hull and the grid (interior wall of the hole) - I was expecting a small gap based on a picture that I saw in another post
- I applied a layer of epoxy on the walls of the hole to create a water tight seal for the portion without the brass insert
- I was concerned that screws might break the fiberglass so I opted for #8 bolts (1.5") with the buts on the inside of the bilge to hold the fitting to the hull - everything sealed with 4200
- I finished off with a removable screen on the side to keep critters out during the winter - sorry, forgot to snap a pic from the inside showing the bolts and the mesh screen
I'll let you know if everything is water-tight when I launch next spring.
Hole as seen from the outside - the hole is ~1" deep (hull + grid)
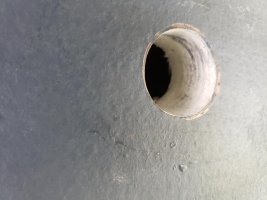
Hole from the outside showing proximity to the keel/hull joint (faint line at the 3" mark on the tape)

From the inside - the bolt is the forward port keel bolt in the main bilge compartment - holes for the 3 bolts not yet drilled
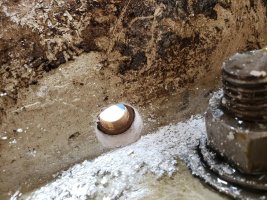
From the outside with 4200 sealant
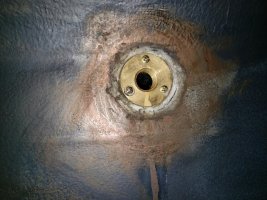